100% waste-based biodiesel seems to be turning into the pariah of alternative fuels. Is it folly to overlook its contribution to CO2 reduction? By Peter Shakespeare and Richard Simpson
The discussion around how to decarbonise road transport has been rumbling on for decades. Today, EU law and the Renewable Transport Fuel Obligation (RTFO) recognise the contribution that renewable fuels such as biodiesel make to decarbonisation – they now make up 7% of the diesel we fill up with at the pump.
Not all the biodiesel used in the UK comes from UK production. The oil refiners buy in a lot of biodiesel from Europe to fulfil their RTFO obligation to add 7% to their mineral-based product. Under the RTFO and European Energy Directive, mass balancing of products is allowed. This means that while the imported biodiesel may be crop based, the same amount of biodiesel must have been produced from waste somewhere in the EU, to offset it. In the UK today, the base stock for biodiesel production comes from waste oils. Crop-based biodiesels are not produced in the UK. Nor is HVO – hydrogenated vegetable oil – a paraffinic drop-in replacement for diesel (www.is.gd/rakoqu). In the UK, Argent Energy, Green Energy and Olleco, are the only producers of 100% – B100 – FAME biodiesel. The annual UK output is 550,000t or 600,000,000 litres.
Higher mineral diesel blends, up to 30% FAME (B30), are available to buy in bulk, and some of the OEMs approve its use in their vehicles, providing the fuel meets B20/B30 production standard EN16709, without any effect on warranty terms (see table, p16). Despite the B100 produced in the UK being 100% renewable and carbon neutral, it would seem its use has not gained real traction. Notably, DAF, Volvo and IVECO do not offer B100 engine options. While MAN, Scania, Mercedes and Renault still support B100, they typically offer limited Euro VI engine options, and those require HVO.
The UK’s biggest producer of B100 FAME is Argent Energy (pictured, above and p16 and p18). Its public affairs director, Dickon Posnett, says that while 100% biodiesel produced from waste vegetable oil is as close to carbon-neutral as a fuel can get, there aren’t many fleet operators using it. So, what is putting people off?
Posnett says: “This is a conversation I have been having with the Low Carbon Vehicle Partnership (LCVP), the Renewable Energy Agency and the DfT over the last few months. I am genuinely puzzled as to why so much effort is going into carbon reduction vehicle trials and all of them are overlooking 100% biodiesel.”
USE CASES
According to Posnett, B100 provides good upper engine lubricity and has a relatively high cetane level, which keeps the particulates down in tailpipe emissions. Carbon monoxide emissions are lower, but NOx emissions are slightly higher, because B100 burns hotter than mineral diesel. But the levels are well within what can be cleaned up by emissions aftertreatment systems.
Those numbers agree with findings from a South American trial. In Argentina, Scania has tried running 100% biodiesel (B100) in trucks and buses (pictured, opposite and p18). Argentinian B100 is made from soy oil, is a mix of fatty acid methyl esters, and requires a different additive package to mineral diesel to avoid issues with low-temperature behaviour and premature oxidisation. During 2016/17, the fuel was trialled in a Euro V RCV operated by CLIBA in Buenos Aires, and compared to an identical vehicle running on conventional diesel on identical routes working 16 hours a day, seven days a week. Special fuel filters were installed to cope with the B100 fuel, and oil condition monitored.
In use, the B100-fuelled truck emitted less visible smoke, and SO2 emissions fell to zero. The engine was quieter, but some drivers complained of a power reduction in the order of 5%. After 250 hours’ running, the engine oil reached the 4% fuel contamination threshold set by Scania, and had to be changed. The normal expectation would be for the oil to last double that.
After over a year of continuous running, the engine was stripped for inspection. The special fuel filters still looked like new, and the valve train clean. All engine bearings were in perfect condition, the crankcase clean, and the fuel injectors clean and in calibration. Emissions tests showed the engine operating easily within Euro V limits: it was producing 1.7 grammes per kW/hr of NOx and 0.02 grammes per kW/hr of PM. It was concluded that, with the oil change precautions followed, Scania engines will work perfectly on B100 fuel conforming to FAME standard EN14214.
Posnett admits that Argent Energy has also witnessed increased fuel consumption, of up to 4%, based on its own B100 fleet and from customers’ experiences. But he argues that fleets should put this fuel consumption premium in due operational context. He says: “It’s important to remember that there are far more severe impacts on it than the thermal efficiency of the fuel. B100 is a renewable fuel and the carbon emission savings are clearly demonstrable, so you are not putting additional CO2 into the atmosphere. In economic terms for the vehicle operator, if the price compensates [for the efficiency loss], which with our product it does, then the net economic benefit is still positive.”
Elsewhere, in Hong Kong, Shell is working on a pilot project with restaurant chain Maxims to refine its used cooking oil to fuel its fleet of more than 100 delivery trucks from two food production plants with B5 (5% biodiesel, amounting to 396,000 litres of biodiesel/year). In the region, Shell sources biodiesel components and blends it with mineral diesel, then sells it at Tai Po Market, Tsing Ye and Hong Kong International Airport stations.
The metropolis of Hong Kong produces 20,000 tonnes of waste cooking oil and 175,000 tonnes of fat trap waste annually, according to Hong Kong government figures. Its plant in Tseung Kwan O, which began production in 2014, makes 200t of biodiesel/day. Five years after waste collection subsidiary ASB Junye was set up in 2013, it claims to recycle more than 50% of the waste oil in Hong Kong.
Anne Yu, retail general manager of Shell Hong Kong, says: “By transforming cooking oil into useable fuel, we can reduce both local waste and CO2 emissions, while providing energy security for Hong Kong.”
And in the oil-rich Middle East, McDonald’s fleet in UAE has covered over five million km on fuel recovered from its waste cooking oil, giving a 99% reduction in CO2. In the UK, around half of McDonald’s outlets recover their cooking oil for fuel to power the delivery fleet.
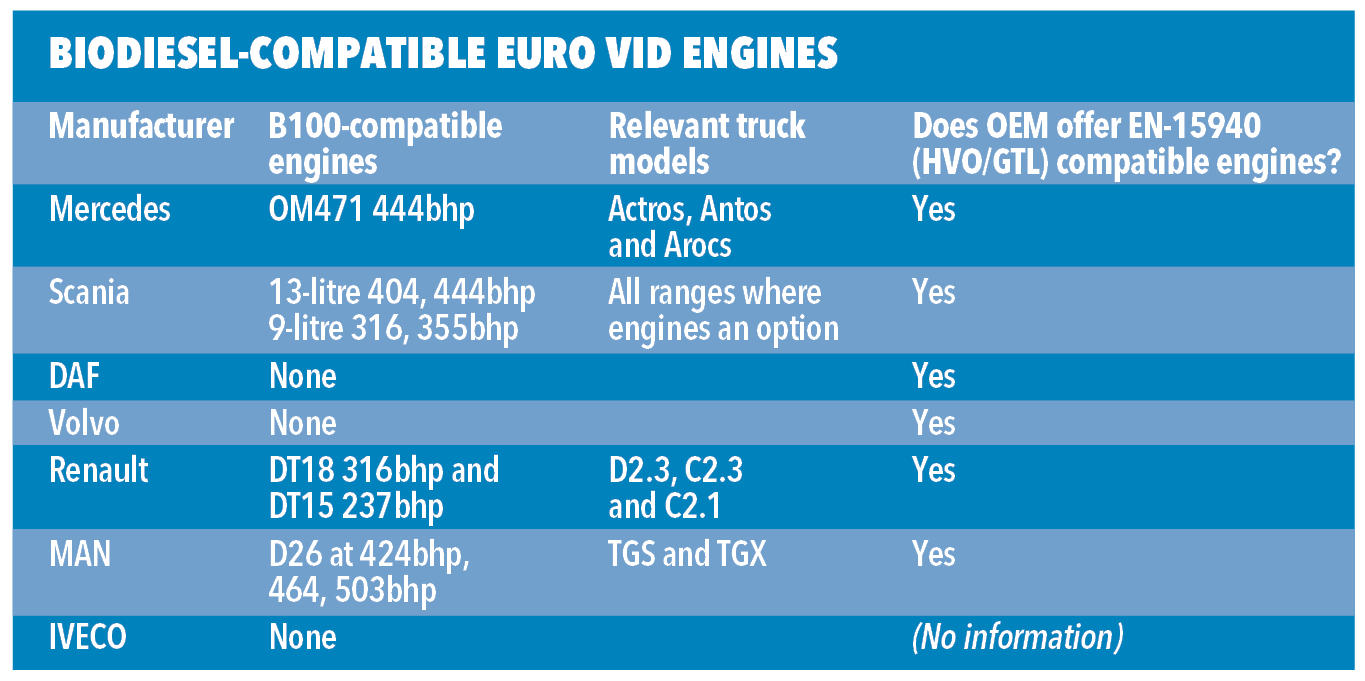
BURNING BIODIESEL
But these gains come with caveats. While all diesel fuel in the UK contains up to 10% biodiesel, and this may rise to 20%, biodiesel can degrade engine lubricants. Andrew Goddard, chairman of oil industry standards body VLS, says: “Increasing use of biodiesel presents challenges for lubricants. Biodiesel, like all fuels, will find its way into the oil sump where it will contribute to oil degradation by increasing the rate of oxidation and increasing the lubricant viscosity. This in turn will increase piston deposits and lead to a higher rates of component wear.
“Biodiesels are more prone to oxidation and the creation of free radicals than mineral diesels. This can lead to the formation of acids in the fuel and the production of insolubles and other sediments that can cause deposits in the fuel system and injectors. Fuel additives can be used to stabilise and enhance biodiesel and biodiesel blends.”
That’s not all, adds Posnett from Argent: “Rubber erosion is another consideration. B100 can corrode certain types of rubber. Most modern vehicles are now fitted with rubber fuel lines and seals that are resistant to degradation by biodiesel. Also, injector settings may need to be changed, and the vehicle’s service intervals are reduced, given the need to change the engine oil and oil and fuel filters more frequently. The other issue is the OEMs will not warranty vehicles with aftermarket conversions, which puts most hauliers off converting to B100.”
ADDITIONAL REQUIREMENTS
While employed to be a champion for his company’s product, Posnett admits that using FAME biodiesel in its unadulterated form poses additional requirements above mineral diesel.
He explains: “B100 storage needs to be managed. With B100, the fuel storage tank needs to be heated to keep the fuel above 10°C. In large tanks, a circulation pump is also required. Insulating and heating a large 70,000-litre storage tank will cost around £30,000. A small tank will be around £5,000. This is a one-off cost and the running costs are minimal, because the heaters and circulation pump are low energy. But because the fuel is kept above 10°C, you don’t get condensation in the tank, so the fuel stays super dry.
“There are other considerations. B100 is not a drop-in replacement, because the cold plug-in point is not as good as standard mineral diesel. Therefore, you must heat the fuel in the vehicle fuel tank in the winter months.” He goes on to explain that there are two ways to do this. A Stagecoach trial of electric heating pads on the vehicle fuel tank proved costly and difficult to administer, partly because the buses had to be plugged in overnight to run the heaters.
“The other method is a system that takes hot engine coolant through heating elements in the fuel tank. On the side of the main tank is a small tank with mineral diesel. This used to start the vehicle. Once the circulated engine coolant warms up the biodiesel in the main tank, a thermostat automatically switches the supply over and you run on the B100. This is the system that the OEMs factory-fit in their new B100 approved vehicles. But it means an older vehicle needs to be converted. The cost to convert is in the region of £4,000 per vehicle.”
COMBAT MISINFORMATION
Posnett argues that a degree of ignorance, misinformation and scepticism surrounds the use, economics and benefits of using B100. He says: “I believe there is an urgent need for fully costed models covering whole-life running costs for all alternative fuels, so all the impacts and implications are transparent.”
Is B100 being written off as a road fuel? Posnett replies: “It is clear there are significant marketing efforts to support other solutions. I believe that DfT thinks because biodiesel is already supported by the RTFO, incentivising it more is unnecessary. But the EU directive or RTFO don’t apply to high blends of biodiesel or B100. Therefore, the vehicle manufacturers are not compelled to produce and support B100-compatible vehicles. The OEMs will change their stance when the pressure is applied, but the RTFO alone is not enough.
“We would love to work with partners to clarify the facts surrounding B100. B100 is a truly renewable ultra-low carbon fuel. We should embrace it.”
BOX: HOW IT IS MADE
B100 is produced by a transesterification process. Posnett at Argent Energy says: “We use the worst grade of waste oil. This is because the technology we use allows us to. Once we have passed the waste oil through fine filters to clean it and put it through the transesterification process, it then goes through a distillation process. This means we get a very clean and pure biodiesel. Other producers don’t, but they start with a much cleaner base oil: something in the region of 5% FFA (free fatty acids). To give you an idea, 5% FFA would be the waste oil that comes out of a McDonald’s restaurant, or the local chip shop. We can start with base oil of 90% FFA. With distillation, you can guarantee the biodiesel has an ultra-low water content and unrecordable levels of monoglycerides – the component in biodiesel that has been blamed for fuel filter clogging. EN14214 (the B100 purity standard) allows 500ppm of water. Our B100 is between 50 and 70ppm. To put this in perspective, the EN590 mineral diesel limit for water is 200ppm.”